Фанера бакелитовая википедия – Фанера — Википедия
Бакелитовая фанера Википедия
Древесно-слоистый пластик (ДСП) Не путать с «Древесно-стружечной плитой», которую также иногда упрощённо обозначают аббревиатурой ДСП, хотя для древесно-стружечных плит имеется своя аббревиатура — ДСтПДреве́сно-слои́стый пластик (ДСП) (лигнофоль, балинит, дельта-древесина) — материал, представляющий собой древесно-полимерный композит, изготавливаемый из листов лущеного шпона (берёзы и других пород, толщиной 0,35—0,65 мм, влажностью 6—10 %), склеенных синтетическими смолами резольного типа под давлением и температурой[1].
Области применения
Антифрикционные свойства, стойкость к воздействию агрессивных сред, абразивов; стабильность при сверхнизких температурах (–270 °С), механическая прочность, водостойкость, диэлектрические свойства позволяют применять ДСП в различных областях техники, таких как:
- Узлы трения.
- Зубчатые колеса.
- Закрытые и открытые металло-полимерные зубчатые передачи.
- Вкладыши подшипников скольжения.
- Для изготовления пуленепробиваемых дверей, банковского оборудования.
- Криогенная и космическая техника.
- В судостроительной промышленности для изготовления дейдвудных подшипников гребных валов.
- Для изготовления затворов гидротехнических сооружений.
- В авиационной технике лопасти; винты вертолётов.
- В транспортном машиностроении: настил полов в автобусах, троллейбусах, трамваях; направляющие эскалаторов метрополитена.
- В строительстве.
- В электротехнической промышленности для изготовления изоляторов, деталей трансформаторов высокого напряжения, выпрямителей (заменяет стеклопластик, текстолит и гетинакс).
- Для изготовления деталей машин текстильной промышленности.
- Как самосмазывающий антифрикционный материал, материал в качестве ползунов лесопильных рам и других аналогичных деталей.
- В металлургическом оборудовании.
- В горнодобывающем оборудовании.
Марки ДСП
В зависимости от расположения волокон древесины шпона в смежных слоях и назначения древесные слоистые пластики в России изготовливают следующих марок:- ДСП-А;
- ДСП-Б; ДСП-Б-э; ДСП-Б-м; ДСП-Б-т; ДСП-Б-о;
- ДСП-В; ДСП-В-э; ДСП-В-м;
- ДСП-Г; ДСП-Г-м.
Буквы А, Б, В, Г указывают порядок укладки шпона в пластике:
- А — волокна древесины шпона во всех слоях имеют параллельное направление или каждые 4 слоя с параллельным направлением волокон древесины шпона чередуются с одним слоем, имеющим направление волокон под углом 20—25° к смежным слоям.
- Б — каждые 8—12 слоев шпона с параллельным направлением волокон древесины шпона чередуются с одним слоем, имеющим перпендикулярное направление волокон древесины к смежным слоям.
- В — волокна древесины шпона в смежных слоях взаимно перпендикулярны.
- Г — волокна древесины шпона в смежных слоях последовательно смещены на угол 45°.
Буквы э, м, т и о определяют назначение материала:
- э — для изготовления конструкционных и электроизоляционных деталей аппаратуры высокого напряжения, электрических машин, трансформаторов, ртутных выпрямителей и т. п.
- м — как самосмазывающий антифрикционный материал, материал в качестве ползунов лесопильных рам и других аналогичных деталей
- т — для изготовления деталей машин текстильной промышленности
- о — как конструкционный и антифрикционный материал.
Размеры
Древесные слоистые пластики изготовляют прямоугольной формы в виде листов толщиной менее 15 мм и плит толщиной 15—60 мм, длиной 700—5600 мм, шириной 950—1500 мм.
Свойства
- Плотность — 1,3 г/см³
- Предел прочности:
- при сжатии — 100—180 МПа
- при растяжении — 140—280 МПа
- при изгибе — 150—280 МПа
- Прочность при скалывании по шву — 11—15 МПа
- Ударная вязкость — 25—80 кДж/м²
- Твердость по Бринеллю — 250 МПа
- Водопоглощение за 24 ч — 5—15 %
- Электрическая прочность:
- поперек слоев — 26—32 МВ/м
- вдоль слоев — 3—13 МВ/м
Древесно-слоистые пластики стойки в трансформаторном масле, уксусном альдегиде, моторном топливе, бутаноле, стироле; нестойки в окислителях, сильных кислотах и щелочах. Перерабатывают в изделия механической обработкой на обычных станках со специальными инструментами.
Технологический процесс изготовления
Получают последовательно пропиткой шпона толщиной 0,3—0,8 мм лиственных пород древесины (обычно березы) фенолоформальдегидной смолой или крезолоформальдегидной смолой в открытых ваннах или автоклавах (0,4—0,8 МПа), сушкой при ступенчатом нагревании до 90 °С, сборкой полученных препрегов в пакеты и прессованием их на этажных прессах (до 20 МПа, 150 °С) и обрезкой в размер.
Примечания
- ↑ ГОСТ 13913-78 «Пластики древесные слоистые (ДСП). Технические условия»
См. также
Литература
- Химический энциклопедический словарь. — М.: Советская энциклопедия, 1983. — 792 с.
- Шейдин И. А., Пюдик П. Э. Технология производства древесных пластиков и их применение. — М., 1971.
- Баженов В. А., Карасев Е. И., Мерсов Е. Д. Технология и оборудование производства древесных плит и пластиков. — М., 1980.
- И. А. Шулепов, Ю. Г. Доронин. Древесные слоистые пластики. — М.: Лесная промышленность, 1987.
- ГОСТ 13913-78 «Пластики древесные слоистые. Технические условия».
- ГОСТ 20966-75 «Пластик древесный слоистый марки ДСП-Б-а. Технические условия».
Ссылки
wikiredia.ru
Бакелит — Википедия
Материал из Википедии — свободной энциклопедии
Текущая версия страницы пока не проверялась опытными участниками и может значительно отличаться от версии, проверенной 20 апреля 2019; проверки требуют 7 правок. Текущая версия страницы пока не проверялась опытными участниками и может значительно отличаться от версии, проверенной 20 апреля 2019; проверки требуют 7 правок. Телефонный аппарат в корпусе из бакелита (1931)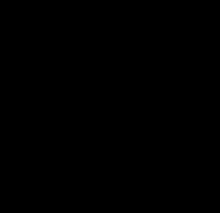
Бакелит (по имени американского химика и изобретателя Лео Бакеланда[1]), полиоксибензилметиленгликольангидрид — продукт поликонденсации фенола с формальдегидом в присутствии щелочного катализатора, резол (из группы фенолформальдегидных смол), термореактопласт. Образуется на начальном этапе синтеза фенолформальдегидной смолы. Вязкая жидкость или твёрдый растворимый легкоплавкий продукт от светло-жёлтого до чёрного цвета[2].
Используется в качестве связующего в производстве абразивных изделий холодного и горячего прессования и вальцевания, а также для других технических целей. Бакелит растворим в спирте, при длительном нагревании переходит в нерастворимую и неплавкую форму. Это свойство бакелита используется при изготовлении пластических масс. Спиртовые растворы бакелита применяют как лаки.
Ноготь на бакелите черты не оставляет. Бакелит плохой проводник тепла, хорошо сопротивляется давлению, трению, толчкам и ударам. По эластичности приближается к целлулоиду. Хорошо поддаётся обработке на токарном станке. Хороший изолятор, его диэлектрическая проницаемость — от 5,6 до 8,85, то есть выше, чем у гуттаперчи и так же велика, как у слюды. Вода, разведённые щелочи и кислоты на бакелит не действуют, лишь горячие концентрированные азотная и серная кислоты его разлаг
ru.wikipedia.org
Дельта-древесина — Википедия
Материал из Википедии — свободной энциклопедии
Текущая версия страницы пока не проверялась опытными участниками и может значительно отличаться от версии, проверенной 29 сентября 2015; проверки требуют 64 правки. Текущая версия страницы пока не проверялась опытными участниками и может значительно отличаться от версии, проверенной 29 сентября 2015; проверки требуют 64 правки. Дельта-древесина, или ДСП-10, или лигнофоль, или балинит — конструкционный композитный материал, древеснослоистый пластик на основе формальдегидной смолы, армированной древесными волокнами. Получался пластификацией древесного шпона (обычно берёзового) путём пропитки его фенол- или крезолоформальдегидной смолой с последующим горячим прессованием под высоким давлением.Дельта-древесина имеет всего в два раза большую, чем обычная древесина, плотность, при этом значительно превосходя её по прочности (она выше, чем у многих алюминиевых сплавов, хотя и ниже, чем у авиационного дюралюмина после термической обработки и искусственного старения). Кроме того, этот материал практически не горюч, обладает абсолютной стойкостью к поражению грибком (гнили) и имеет длительный срок службы без потери качеств (десятки лет в неблагоприятных условиях
Дельта-древесину не следует путать с водостойкой бакелитизированной фанерой (марок ФБС, ФБС-А, ФБВ), которая представляет собой обычную фанеру с пропиткой спиртовым или водным раствором фенол-формальдегидной смолы, часто даже не на всю толщину пакета.
Во второй половине 1930‑х годов возможности древесины в качестве авиационного конструкционного материала оказались фактически исчерпаны — дальнейшее повышение лётных и тактико-технических характеристик боевых самолётов потребовало освоения принципиально новых материалов, имеющих более выгодное соотношение массы и прочности. Наиболее перспективны в этом отношении были высокопрочные сплавы на основе алюминия (д
ru.wikipedia.org
Что такое бакелитовая фанера? Определение «бакелитовый» материал
Главные характеристики бакелитовой фанеры и ее преимущества для отделки дома
Википедия дает не только определение бакелитовой фанеры как прочного строительного материала для отделки внутренней и внешней частей стен дома, так и дополнительно указывает ее свойства.
Изготовление бакелитовых пластин устроено по методике пластификации шпона древесины сосны или березы. Это происходит под давлением высокого градуса и одновременного давления низкой температуры. Отдельные слои древесного шпона обрабатываются бакелитовым раствором или лакосодержащим веществом. По внешним признакам бакелитовая смесь напоминает смолянистую жидкость, схожую с эбонитом.
По своим характеристикам материал имеет преимущества:
- Не подвергается преждевременному изнашиванию.
- Надежность, высокая прочность.
- Не является воспламеняемой основой.
- Не чувствителен к перепадам температуры.
- Легко переносит влагу и сухость воздуха.
- Не подвергается внешним раздражающим факторам.
- Имеет длительный срок своего использования. Проверено специальной практикой.
- Не имеет в составе вредные вещества, способные навредить здоровью человека. При увеличении температуры не выделяет токсинов.
- Отсутствует подверженность ржавчине и прочих неприятных процессов.
- Имеет внушительный вес. Это в разы увеличивает прочность конструкции из бакелитовой фанеры.
- Имеет стандартные параметры при продаже – толщина 0,5 сантиметров.
Область использования бакелитового материала
Бакелитовая фанера начала свое активное применение в строительстве. Постепенно расширила область использования:
- Строение кораблей, катеров и прочего морского транспорта;
- Автомобилестроении – активно применяется в обустройстве пола в автобусах, машинах;
- Самолетостроении;
- Обустройстве напольного покрытия;
- Производство стендов, настенных вывесок, мишени для тира;
- Мебельном производстве;
- Ремонтных работах квартир;
- Кровельных работах;
- Производство детских игрушек.
Классификация бакелитовой фанеры
Бывает нескольких разновидностей:
- Фанера серии ФБС. Обработка шпон происходит посредством спиртовых смол. Может иметь типы классов ФБС-1, класса «А», «А-1». ФБС отличается своими прочными качествами, не имеет склонности к самовозгоранию.
- ФВБ на основе смол водорастворимых основ. Его марка ФБВ-1.
Как используют бакелитовую фанеру?
Бакелитовую фанеру применяют при ремонтных работах – внутренней и внешней обшивке стен дома.
Она во многом способствует утеплению помещения и созданию прочного каркаса здания. Она фиксируется на подготовленные бетонные поверхности благодаря мастикам:
- Перед использованием бакелитовую конструкцию покрывают определенными лакокрасящими средствами, водонепроницаемыми растворами.
- Поверхность стен затирается, устраняются все неровности и погрешности штукатурки.
- Фанера тщательно фиксируется к стенам.
- Стыки прочно закрываются.
При выборе бакелитовой фанеры стоит проконсультироваться со специалистом. Существует огромный выбор подобного материала. Важно не прогадать при покупке.
ogodom.ru
Фанера Википедия
Схема процесса изготовления фанерыФане́ра (др.-греч. φανερῶς «явный»), древе́сно-сло́истая плита́ — многослойный строительный материал, изготавливаемый путём склеивания специально подготовленного шпона. Для повышения прочности фанеры слои шпона накладываются так, чтобы волокна древесины каждого листа были перпендикулярны соседним, поэтому, чтобы направления внешних слоёв совпадали, количество слоёв шпона обычно нечётное: от трёх и более.
Применение
Самодельный вездеход «Каракат» с кузовом из фанерыСтроительство
Классификация
Фанера называется продольной, если волокна в лицевых слоях направлены вдоль длинной стороны, в противном случае — поперечной.
Фанера из древесины как твёрдых, так и мягких пород выпускается нескольких типов и сортов, которые различаются назначением, сроком службы, внешним видом и стоимостью.
По предназначению — строительная, промышленная, упаковочная, мебельная и конструкционная.
По видам фанеру часто разделяют на два популярных вида — ФК (влагостойкая) и ФСФ (повышенной влагостойкости).
По типу обработки — ламинированная.
По внешнему виду (согласно ГОСТ 3916.1-96) (определяется количеством пороков и дефектов поверхности наружного слоя шпона): E (элита), I, II, III, IV.
По материалу, из которого изготовляется
- Хвойная фанера (изготавливается из шпона хвойных пород деревьев: лиственницы, сосны, пихты, ели). Иногда для изготовления фанеры используется шпон сибирского кедра — такая фанера используется в декоративных целях. Для хвойной фанеры обязательным является содержание хвойного шпона в наружных слоях — внутренние могут содержать шпон лиственных пород древесины.
- Берёзовая фанера (изготавливается из шпона берёзы) получила распространение практически во всех областях, но из-за относительно более высокой стоимости в строительстве используется не так широко, как хвойная.
- Фанера из тополя, которая производится преимущественно в Китае, существенно дешевле российских аналогов из берёзы и хвойных пород, однако уступает им по параметрам[источник не указан 779 дней].
По количеству слоёв
Фанерные слои- трёхслойная
- пятислойная
- многослойная
В основном листы фанеры имеют нечётное количество слоёв шпона: в этом случае шпон расположен симметрично относительно среднего слоя. Если слоёв шпона в фанере четыре, то центральные слои располагают и склеивают перпендикулярно наружным, что увеличивает общую прочность и стойкость к деформации.
По пропитке
Водостойкая фанера — материал, обработанный специальным образом для увеличения сопротивления влаге. Максимально увеличить влагостойкие характеристики фанеры может помочь ламинирование.
- ФБА — это листы фанеры, которые проклеены натуральным альбуминоказеиновым клеем. Преимущество фанеры ФБА в том, что она является экологически чистым строительным материалом, но её небольшая влагостойкость ограничивает применения этой марки.
- ФСФ (фанера, изготавливаемая с применением смоляного фенолформальдегидного клея). Эта фанера характеризуется относительно высокой износоустойчивостью, механической прочностью и высокой водостойкостью. ФСФ — один из самых популярных видов фанеры, используется в строительстве, производстве, кровельных работах. Допускается для применения в жилых помещениях, если класс эмиссии не превышает Е1.
- ФСФ-ТВ (фанера огнезащищённая). Обладает свойствами фанеры марки ФСФ, но не подверженная горению, относится к группе трудногорючих материалов. Применяется в пассажирском вагоностроении и промышленном/гражданском строительстве.
- ФК (фанера, получаемая при приклеивании шпонов карбамидным клеем). Обладая меньшими водостойкими характеристиками, ФК используется преимущественно при внутренней отделке помещений, в мебельном производстве, при изготовлении деревянной тары, при работе с конструкциями внутри помещения.
- ФКМ. В качестве клея при производстве фанеры ФКМ используются меламиновые и меламиноформальдегидные смолы.
- ФБ (фанера, пропитанная бакелитовым лаком, впоследствии склеивается). Этот вид обладает максимальной сопротивляемостью воздействию агрессивной среды и может использоваться в условиях тропического климата, при повышенной влажности и даже под водой.
- БС (фанера, пропитанная бакелитовым клеем, С — спирторастворимый). Эта фанера обладает уникальными свойствами — сверхвысокой прочностью, стойкостью к агрессивным средам, гибкостью, упругостью, водонепроницаема, не гниёт, не раскисает. Её ещё называют авиационная фанера за то, что раньше использовалась только в авиа- и судостроении.
- БВ (фанера, пропитанная бакелитовым клеем, В — водорастворимый). Эта фанера обладает теми же свойствами, что и фанера БС, за исключением влагостойкости, поскольку клей, применяемый при склеивании слоев, водорастворим.
По виду обработки поверхностей
- НШ — нешлифованная фанера.
- Ш1 — материал, шлифованный с одной стороны.
- Ш2 — материал шлифованный с двух сторон.
Виды и сорта фанеры
В настоящий момент ГОСТы предусматривают наличие пяти сортов фанеры, которые отличаются наличием и количеством допустимых дефектов обработки[1], пороков древесины и её дефектов.
Нормы ограничения пороков древесины и дефектов обработки
Наименование пороков древесины и дефектов обработки по ГОСТ 30427 | Фанера с наружными слоями из шпона сортов | ||||
E (элитная) | I сорт (B) | II сорт (BB) | III сорт (CP) | IV сорт (C) | |
1. Булавочные сучки | Не допускаются | Допускаются до 3-х штук на 1 м² поверхности листа | Допускаются | ||
2. Здоровые сросшиеся светлые и тёмные сучки | Не допускаются | Допускаются диаметром, мм, не более | Допускаются с трещинами шириной не более 1,5 мм | Допускаются | |
15 | 25 | ||||
в количестве на 1 м², шт., не более | |||||
5 | 10 | ||||
с трещинами шириной, мм, не более | |||||
0,5 | 1,0 | ||||
3. Частично сросшиеся, несросшиеся, выпадающие сучки, отверстия от них, червоточина | Не допускаются | Допускаются диаметром, мм, не более | |||
6 | 6 | 6 | 40 | ||
в количестве на 1 м² поверхности листа, шт., не более | без ограничения количества | ||||
3 | 6 | 10 | |||
4. Сомкнутые трещины | Не допускаются | Допускаются длиной, не более 200 мм в количестве не более 2 шт., на 1 м ширины листа | Допускаются | ||
5. Разошедшиеся трещины | Не допускаются | Допускаются длиной, мм, не более | |||
200 | 300 | без ограничения | |||
шириной, мм, не более | |||||
2 | 2 | 10 | |||
в количестве, шт., не более | |||||
2 | 2 | без ограничения | |||
при условии заделки замазками | Допускаются длиной до 600 мм, шириной до 5 мм при условии заделки замазкой | ||||
6. Светлая прорость | Не допускается | Допускается | |||
7. Тёмная прорость | Не допускается | Допускается в общем числе с нормами п. 2 настоящей таблицы | Допускается | ||
8. Отклонение в строении древесины | Допускается незначительное случайного характера, кроме тёмных глазков | Допускается | |||
9. Здоровое изменение окраски | Не допускается | Допускается не более, %, поверхности листа 5 | Допускается | ||
10. Нездоровое изменение окраски | Не допускается | Допускается | |||
11. Гниль | Не допускается | ||||
12. Наклон | Не допускается | Допускаются в общем числе с нормами п. 3 настоящей таблицы | |||
13. Нахлёстка в наружных слоях | Не допускается | Допускается длиной, мм, не более | Допускается | ||
100 | 200 | ||||
в количестве, шт., не более | |||||
1 | 2 | ||||
на 1 м ширины листа | |||||
14. Недостача шпона, дефекты кромок листа при шлифовании и обрезке | Не допускаются | Допускаются шириной, мм | |||
15. Наличие клеевой ленты | Не допускается | Допускается в нешлифованной фанере | |||
16. Просачивание клея | Не допускается | Допускается, %, не более | Допускается | ||
2 | 5 | ||||
поверхности листа | |||||
17. Царапины | Не допускаются | Допускаются | |||
18. Вмятина, отпечаток, гребешок | Не допускаются | Допускаются глубиной (высотой) в пределах значений предельных отклонений по толщине | Допускается | ||
19. Вырыв волокон | Не допускается | Допускается, %, поверхности листа, не более | Допускается | ||
5 | 15 | ||||
20. Прошлифовка | Не допускается | Допускается | |||
21. Покоробленность | В фанере толщиной до 6,5 мм не учитывается, толщиной 6,5 мм и более допускается со стрелой прогиба не более 15 мм на 1 м длины диагонали листа фанеры | ||||
22. Металлические включения | Не допускаются | Допускаются скобки из цветного металла | |||
23. Зазор в соединениях | Не допускается | Допускается шириной, мм, не более | Допускается | ||
1 | 2 | ||||
в количестве, шт., не более | |||||
1 | 1 | ||||
на 1 м ширины листа | |||||
24. Расслоение, пузыри, закорина | Не допускаются | ||||
25. Волнистость (для шлифованной фанеры), ворсистость, рябь | Не допускаются | Допускаются | |||
26. Шероховатость поверхности | Параметр шероховатости Rm по ГОСТ 7016, мкм, не более: для шлифованной фанеры — 100, для не шлифованной — 200 | ||||
27. Вставки из древесины | Не допускаются | Допускаются при заделке в количестве, шт., не более | |||
8 на 1 м2листа | без ограничения | ||||
28. Двойная вставка | Не допускается | Допускается, шт., не более 2 на 1 м² листа | Допускается без ограничения | ||
Примечания: 1. Норма дефекта обработки «недостача шпона» относится и к внутренним слоям фанеры. |
Общими словами:
- сорт Е (элита). Дефекты не допускаются, кроме незначительных изменений случайного характера в строении древесины;
- сорт I. Максимальная длина покоробленности или трещин для фанеры первого сорта не должна превышать 20 мм;
- сорт II. Допускаются трещины до 200 мм, вставки из древесины, просачивание клея площадью до 2 % от общей площади листа фанеры;
- сорт III. Допускаются червоточины до 10 штук на квадратный метр при диаметре каждой не более 6 мм; общее количество перечисленных пороков не может быть больше 9;
- сорт IV. Фанера 4-го сорта является крайне низкокачественной. Такая фанера может иметь следующие пороки: частично сросшиеся и выпавшие сучки — без ограничения; червоточины диаметром до 40 мм без ограничения; дефекты кромок листа глубиной до 5 мм;
Технология изготовления
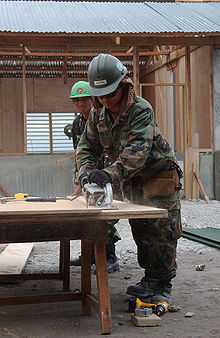
В технологическом процессе производства фанеры можно ориентировочно выделить 14 этапов:
1) Подготовка сырья к лущению.
На начальном этапе происходит отбор качественного берёзового фанерного кряжа, он должен соответствовать ГОСТу 9462-88. По поступлении на завод сырьё гидротермически обрабатывается в варочных бассейнах.
2) Окорка сырья.
Окорка — удаление с поверхности кряжа коры и луба. После произведения окорки бревна прогоняют через специальный сканер, определяющий кубатуру кряжа.
3) Разделка фанерного сырья.
Для разделки сырья на чураки используется пильный агрегат, работающий в полуавтоматическом режиме. Получившиеся от разделки под определённую ширину листа отходы отправляются в отделение переработки отходов, а сырьё в виде чураков — в приёмник-накопитель и на следующий этап, к лущильному станку.
4) Лущение, рубка и укладка шпона.
Для лущения шпона используются лущильные станки, а рубка по размерам осуществляется ножницами, получаемый шпон в сыром виде на выходе имеет толщину в 1,15—1,18 мм. Получившаяся после лущения лента шпона подаётся к пневматическим ножницам, для раскроя на форматные листы в полуавтоматическом режиме. Лущёный шпон стопками подаётся к сушилке.
5) Сушка шпона.
Сушится шпон с использованием газовых роликовых сушилок, работающих на топочных газах, а также и в термомасляной сушилке.
6) Сортировка шпона.
После сушки шпон делится на несколько частей, одна из которых направляется на ребросклеивание и шпонопочинку, а другая — сразу на сортировку в соответствии с требованиями ГОСТ 3916.1-96 или требованиями заказчика. Неформатный, кусковой и оставшийся от обрезки шпон отправляется на ребросклеивание вдоль волокон на внутренние слои, а после обрезки поперёк — на линию усовки.
7) Склеивание шпона на «ус».
Склеенный на «ус» поперёк волокон шпон идёт на внутренние слои большеформатной фанеры.
8) Ребросклеивание шпона.
Для ребросклейки используются станки с подачей шпона вдоль и поперёк древесных волокон.
9) Починка шпона.
В починку шпона идут полоски шпона шириной до 49 мм, они подбираются по направлению волокон, цвету и породе древесины, толщине относительно требующих починки листов и плотно держатся в шпоне.
10) Приготовление и нанесение клея.
Рецептура приготовления клея — секрет производства любого фанерного завода, а наносится клей на шпон клеенаносящими станками, с помощью рифлёных металлических барабанов строго цилиндрической формы.
11) Сборка пакетов.
Шпон с нанесенным клеем отправляют в наборку, где собираются пакеты, которые, проходя холодную подпрессовку, формируют будущие листы фанеры. Пакеты собираются в угольник, прижимаясь к упорам с двух сторон наборного стола. После холодной подпрессовки пакеты отправляют в загрузку горячего пресса.
12) Склеивание фанеры.
Для склеивания фанеры используется горячий гидравлический пресс с электронной системой управления прессованием, механической загрузкой и выгрузкой. После пресса фанера развозится погрузчиком в стопы для выстройки. Стопы держатся в течение 24 часов в условиях цеха чтобы снять внутренние напряжения.
13) Обрезка фанеры и шлифование.
В обрезке фанеры используются форматно-обрезные станки, а после обрезки её автопогрузчиком подают на сортировку или шлифовальный станок.
14) Сортировка, маркировка и упаковка.
Фанера подается на сортировочные площадки после обрезки и шлифования, где сортируется по ГОСТу 3916.1-96, после чего производится маркировка листов фанеры, упаковка её в стандартные транспортировочные пачки и маркировка пачек.
Производство в России
Фанера в России выпускается следующих основных форматов 1525×1525, 1220×2440, 2440×1220, 1250×2500, 2500×1250, 1500×3000, 3000×1500, 1525×3050 и 3050×1525 мм. Различие в расположении длины и ширины относительно формата фанеры обозначает продольное или поперечное расположение волокон шпона по длинной стороне и указывает, что если формат заявлен как 1220×2440 мм, то расположение слоёв шпона поперечное, а если 2440×1220 мм — продольное. Фанера с продольным расположением волокон шпона используется там, где требуется гибкость, а с поперечным — там, где требуется высокая жёсткость при изгибе.
Производство фанеры в России (млн. м³):
- 2002 г. — 1,8;
- 2003 г. — 2,0;
- 2004 г. — 2,2;
- 2005 г. — 2,6;
Фанерное производство в России расположено по большей части в привязке к регионам, богатым лесными ресурсами. Основная доля выпуска приходится на предприятия Северо-Западного федерального округа — около 35 % в общем объёме производства.
В 2005 году экспорт составил 1,5 млн м³, то есть около 60 % всей произведённой в стране фанеры.
См. также
Примечания
Литература
- Григорьев М. А. Материаловедение для столяров, плотников и паркетчиков: Учебное пособие для ПТУ. — М.: Высшая школа, 1989. — 223 с. — 100 000 экз. — ISBN 5-06-000345-0.
- ГОСТ 3916.1-96 Фанера общего назначения с наружными слоями из шпона лиственных пород.
- ГОСТ 3916.2-96 Фанера общего назначения с наружными слоями из шпона хвойных пород.
- ГОСТ 13913-78 (ГОСТ на ДСП)
- ГОСТ 102-75 Фанера берёзовая авиационная.
- ГОСТ В-226-41 Дельта-древесина авиационная.
Ссылки
- Черкасов И. К. Фанера // БСЭ
wikiredia.ru
Бакелитовая фанера Википедия
Древесно-слоистый пластик (ДСП) Не путать с «Древесно-стружечной плитой», которую также иногда упрощённо обозначают аббревиатурой ДСП, хотя для древесно-стружечных плит имеется своя аббревиатура — ДСтПДреве́сно-слои́стый пластик (ДСП) (лигнофоль, балинит, дельта-древесина) — материал, представляющий собой древесно-полимерный композит, изготавливаемый из листов лущеного шпона (берёзы и других пород, толщиной 0,35—0,65 мм, влажностью 6—10 %), склеенных синтетическими смолами резольного типа под давлением и температурой[1].
Области применения[ | ]
Антифрикционные свойства, стойкость к воздействию агрессивных сред, абразивов; стабильность при сверхнизких температурах (–270 °С), механическая прочность, водостойкость, диэлектрические свойства позволяют применять ДСП в различных областях техники, таких как:
- Узлы трения.
- Зубчатые колеса.
- Закрытые и открытые металло-полимерные зубчатые передачи.
- Вкладыши подшипников скольжения.
- Для изготовления пуленепробиваемых дверей, банковского оборудования.
- Криогенная и космическая техника.
- В судостроительной промышленности для изготовления дейдвудных подшипников гребных валов.
- Для изготовления затворов гидротехнических сооружений.
- В авиационной технике лопасти; винты вертолётов.
- В транспортном машиностроении: настил полов в автобусах, троллейбусах, трамваях; направляющие эскалаторов метрополитена.
- В строительстве.
- В электротехнической промышленности для изготовления изоляторов, деталей трансформаторов высокого напряжения, выпрямителей (заменяет стеклопластик, текстолит и гетинакс).
- Для изготовления деталей машин текстильной промышленности.
- Как самосмазывающий антифрикционный материал, материал в качестве ползунов лесопильных рам и других аналогичных деталей.
- В металлургическом оборудовании.
- В горнодобывающем оборудовании.
Марки ДСП[ | ]
В зависимости от расположения волокон древесины шпона в смежных слоях и назначения древесные слоистые пластики в России изготовливают следующих марок:
- ДСП-А;
- ДСП-Б; ДСП-Б-э; ДСП-Б-м; ДСП-Б-т; ДСП-Б-о;
- ДСП-В; ДСП-В-э; ДСП-В-м;
- ДСП-Г; ДСП-Г-м.
Буквы А, Б, В, Г указывают порядок укладки шпона в пластике:
- А — волокна древесины шпона во всех слоях имеют параллельное направление или каждые 4 слоя с параллельным направлением волокон древесины шпона чередуются с одним слоем, имеющим направление волокон под углом 20—25° к смежным слоям.
- Б — каждые 8—12 слоев шпона с параллельным направлением волокон древесины шпона чередуются с одним слоем, имеющим перпендикулярное направление волокон древесины к смежным слоям.
- В — волокна древесины шпона в смежных слоях взаимно перпендикулярны.
- Г — волокна древесины шпона в смежных слоях последовательно смещены на угол 45°.
Буквы э, м, т и о определяют назначение материала:
- э — для изготовления конструкционных и электроизоляционных деталей аппаратуры высокого напряжения, электрических машин, трансформаторов, ртутных выпрямителей и т. п.
- м — как самосмазывающий антифрикционный материал, материал в качестве ползунов лесопильных рам и других аналогичных деталей
- т — для изготовления деталей машин текстильной промышленности
- о — как конструкционный и антифрикционный материал.
Размеры[
ru-wiki.ru
Фанера — Википедия. Что такое Фанера
Схема процесса изготовления фанерыФане́ра (древе́сно-сло́истая плита́) (др.-греч. φανερός — явный) — многослойный строительный материал, изготавливаемый путём склеивания специально подготовленного шпона. Количество слоёв шпона обычно нечётное, от 3 и более. Для повышения прочности фанеры слои шпона накладываются так, чтобы волокна древесины были строго перпендикулярны предыдущему листу.
Применение
Самодельный вездеход «Каракат» с кузовом из фанерыСтроительство
Классификация
Фанера называется продольной, если волокна в лицевых слоях направлены вдоль длинной стороны, в противном случае — поперечной.
Фанера из древесины как твёрдых, так и мягких пород выпускается нескольких типов и сортов, которые различаются назначением, сроком службы, внешним видом и стоимостью.
По предназначению — строительная, промышленная, упаковочная, мебельная и конструкционная.
По видам фанеру часто разделяют на два популярных вида — ФК (влагостойкая) и ФСФ (повышенной влагостойкости).
По типу обработки — ламинированная.
По внешнему виду (согласно ГОСТ 3916.1-96) (определяется количеством пороков и дефектов поверхности наружного слоя шпона): E (элита), I, II, III, IV.
По материалу, из которого изготовляется
- Хвойная фанера (изготавливается из шпона хвойных пород деревьев: лиственницы, сосны, пихты, ели). Иногда для изготовления фанеры используется шпон сибирского кедра — такая фанера используется в декоративных целях. Для хвойной фанеры обязательным является содержание хвойного шпона в наружных слоях — внутренние могут содержать шпон лиственных пород древесины.
- Берёзовая фанера (изготавливается из шпона берёзы) получила распространение практически во всех областях, но из-за относительно более высокой стоимости в строительстве используется не так широко, как хвойная.
- Фанера из тополя, которая производится преимущественно в Китае, существенно дешевле российских аналогов из берёзы и хвойных пород, однако уступает им по параметрам[источник не указан 477 дней].
По количеству слоев
Фанерные слои- трёхслойная
- пятислойная
- многослойная
В основном листы фанеры имеют нечётное количество слоёв шпона: в этом случае шпон расположен симметрично относительно среднего слоя. Если слоёв шпона в фанере четыре, то центральные слои располагают и склеивают перпендикулярно наружным, что увеличивает общую прочность и стойкость к деформации.
По пропитке
Водостойкая фанера — материал, обработанный специальным образом для увеличения сопротивления влаге. Максимально увеличить влагостойкие характеристики фанеры может помочь ламинирование.
- ФБА — это листы фанеры, которые проклеены натуральным альбуминоказеиновым клеем. Преимущество фанеры ФБА в том, что она является экологически чистым строительным материалом, но её небольшая влагостойкость ограничивает применения этой марки.
- ФСФ (фанера, изготавливаемая с применением смоляного фенолформальдегидного клея). Эта фанера характеризуется относительно высокой износоустойчивостью, механической прочностью и высокой водостойкостью. ФСФ — один из самых популярных видов фанеры, используется в строительстве, производстве, кровельных работах. Допускается для применения в жилых помещениях, если класс эмиссии не превышает Е1.
- ФСФ-ТВ (фанера огнезащищенная). Обладает свойствами фанеры марки ФСФ, но не подверженная горению, относится к группе трудногорючих материалов. Применяется в пассажирском вагоностроении и промышленном/гражданском строительстве.
- ФК (фанера, получаемая при приклеивании шпонов карбамидным клеем). Обладая меньшими водостойкими характеристиками, ФК используется преимущественно при внутренней отделке помещений, в мебельном производстве, при изготовлении деревянной тары, при работе с конструкциями внутри помещения.
- ФКМ. В качестве клея при производстве фанеры ФКМ используются меламиновые и меламиноформальдегидные смолы.
- ФБ (фанера, пропитанная бакелитовым лаком, впоследствии склеивается). Этот вид обладает максимальной сопротивляемостью воздействию агрессивной среды и может использоваться в условиях тропического климата, при повышенной влажности и даже под водой.
- БС (фанера, пропитанная бакелитовым клеем, С — спирторастворимый). Эта фанера обладает фантастическими свойствами — сверхвысокой прочностью, стойкостью к агрессивным средам, гибкостью, упругостью, водонепроницаема, не гниёт, не раскисает. Её ещё называют авиационная фанера за то, что раньше использовалась только в авиа- и судостроении.
- БВ (фанера, пропитанная бакелитовым клеем, В — водорастворимый). Эта фанера обладает теми же свойствами, что и фанера БС, за исключением влагостойкости, поскольку клей, применяемый при склеивании слоев, водорастворим.
По виду обработки поверхностей
- НШ — нешлифованная фанера
- Ш1 — материал, шлифованный с одной стороны
- Ш2 — материал шлифованный с двух сторон
Виды и сорта фанеры
В настоящий момент ГОСТы предусматривают наличие пяти сортов фанеры, которые отличаются наличием и количеством допустимых дефектов обработки[1], пороков древесины и её дефектов.
Нормы ограничения пороков древесины и дефектов обработки
Наименование пороков древесины и дефектов обработки по ГОСТ 30427 | Фанера с наружными слоями из шпона сортов | ||||
E (элитная) | I сорт | II сорт | III сорт | IV сорт | |
1. Булавочные сучки | Не допускаются | Допускаются до 3 шт. на 1 м² поверхности листа | Допускаются | ||
2. Здоровые сросшиеся светлые и темные сучки | Не допускаются | Допускаются диаметром, мм, не более | Допускаются с трещинами шириной не более 1,5 мм | Допускаются | |
15 | 25 | ||||
в количестве на 1 м², шт., не более | |||||
5 | 10 | ||||
с трещинами шириной, мм, не более | |||||
0,5 | 1,0 | ||||
3. Частично сросшиеся, несросшиеся, выпадающие сучки, отверстия от них, червоточина | Не допускаются | Допускаются диаметром, мм, не более | |||
6 | 6 | 6 | 40 | ||
в количестве на 1 м² поверхности листа, шт., не более | без ограничения количества | ||||
3 | 6 | 10 | |||
4. Сомкнутые трещины | Не допускаются | Допускаются длиной, не более 200 мм в количестве не более 2 шт., на 1 м ширины листа | Допускаются | ||
5. Разошедшиеся трещины | Не допускаются | Допускаются длиной, мм, не более | |||
200 | 300 | без ограничения | |||
шириной, мм, не более | |||||
2 | 2 | 10 | |||
в количестве, шт., не более | |||||
2 | 2 | без ограничения | |||
при условии заделки замазками | Допускаются длиной до 600 мм, шириной до 5 мм при условии заделки замазкой | ||||
6. Светлая прорость | Не допускается | Допускается | |||
7. Темная прорость | Не допускается | Допускается в общем числе с нормами п. 2 настоящей таблицы | Допускается | ||
8. Отклонение в строении древесины | Допускается незначительное случайного характера, кроме темных глазков | Допускается | |||
9. Здоровое изменение окраски | Не допускается | Допускается не более, %, поверхности листа 5 | Допускается | ||
10. Нездоровое изменение окраски | Не допускается | Допускается | |||
11. Гниль | Не допускается | ||||
12. Наклон | Не допускается | Допускаются в общем числе с нормами п. 3 настоящей таблицы | |||
13. Нахлёстка в наружных слоях | Не допускается | Допускается длиной, мм, не более | Допускается | ||
100 | 200 | ||||
в количестве, шт., не более | |||||
1 | 2 | ||||
на 1 м ширины листа | |||||
14. Недостача шпона, дефекты кромок листа при шлифовании и обрезке | Не допускаются | Допускаются шириной, мм | |||
15. Наличие клеевой ленты | Не допускается | Допускается в нешлифованной фанере | |||
16. Просачивание клея | Не допускается | Допускается, %, не более | Допускается | ||
2 | 5 | ||||
поверхности листа | |||||
17. Царапины | Не допускаются | Допускаются | |||
18. Вмятина, отпечаток, гребешок | Не допускаются | Допускаются глубиной(высотой) в пределах значений предельных отклонений по толщине | Допускается | ||
19. Вырыв волокон | Не допускается | Допускается, %, поверхности листа, не более | Допускается | ||
5 | 15 | ||||
20. Прошлифовка | Не допускается | Допускается | |||
21. Покоробленность | В фанере толщиной до 6,5 мм не учитывается, толщиной 6,5 мм и более допускается со стрелой прогиба не более 15 мм на 1 м длины диагонали листа фанеры | ||||
22. Металлические включения | Не допускаются | Допускаются скобки из цветного металла | |||
23. Зазор в соединениях | Не допускается | Допускается шириной, мм, не более | Допускается | ||
1 | 2 | ||||
в количестве, шт., не более | |||||
1 | 1 | ||||
на 1 м ширины листа | |||||
24. Расслоение, пузыри, закорина | Не допускаются | ||||
25. Волнистость (для шлифованной фанеры), ворсистость, рябь | Не допускаются | Допускаются | |||
26. Шероховатость поверхности | Параметр шероховатости Rm по ГОСТ 7016, мкм, не более: для шлифованной фанеры — 100, для не шлифованной — 200 | ||||
27. Вставки из древесины | Не допускаются | Допускаются при заделке в количестве, шт., не более | |||
8 на 1 м2листа | без ограничения | ||||
28. Двойная вставка | Не допускается | Допускается, шт., не более 2 на 1 м2 листа | Допускается без ограничения | ||
Примечания: 1. Норма дефекта обработки «недостача шпона» относится и к внутренним слоям фанеры. |
Общими словами
- сорт Е (элита). Дефекты не допускаются, кроме незначительных изменений случайного характера в строении древесины;
- сорт I. Максимальная длина покоробленности или трещин для фанеры первого сорта не должна превышать 20 мм;
- сорт II. Допускаются трещины до 200 мм, вставки из древесины, просачивание клея площадью до 2 % от общей площади листа фанеры;
- сорт III. Допускаются червоточины до 10 шт. на квадратный метр при диаметре каждой не более 6 мм; общее количество перечисленных пороков не может быть больше 9;
- сорт IV. Фанера 4 сорта является крайне низкокачественной. Такая фанера может иметь следующие пороки: частично сросшиеся и выпавшие сучки — без ограничения; червоточины диаметром до 40 мм без ограничения; дефекты кромок листа глубиной до 5 мм;
Технология изготовления
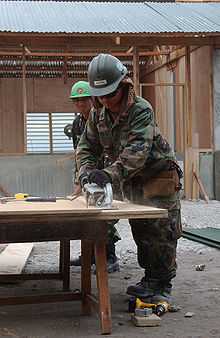
В технологическом процессе производства фанеры можно ориентировочно выделить 14 этапов, рассмотрим их по порядку:
1) Подготовка сырья к лущению
На начальном этапе происходит отбор качественного берёзового фанерного кряжа, он должен соответствовать ГОСТу 9462-88. По поступлении на завод сырьё гидротермически обрабатывается в варочных бассейнах.
2) Окорка сырья
Окорка — удаление с поверхности кряжа коры и луба. После произведения окорки бревна прогоняют через специальный сканер, определяющий кубатуру кряжа.
3) Разделка фанерного сырья
Для разделки сырья на чураки используется пильный агрегат, работающий в полуавтоматическом режиме. Получившиеся от разделки под определенную ширину листа отходы отправляются в отделение переработки отходов, а сырьё в виде чураков — в приемник-накопитель и на следующий этап, к лущильному станку.
4) Лущение, рубка и укладка шпона
Для лущения шпона используются лущильные станки, а рубка по размерам осуществляется ножницами, получаемый шпон в сыром виде на выходе имеет толщину в 1,15—1,18 мм. Получившаяся после лущения лента шпона подаётся к пневматическим ножницам, для раскроя на форматные листы в полуавтоматическом режиме. Лущёный шпон стопками подаётся к сушилке.
5) Сушка шпона
Сушится шпон с использованием газовых роликовых сушилок, работающих на топочных газах, а также и в термомасляной сушилке.
6) Сортировка шпона
После сушки шпон делится на несколько частей, одна из которых направляется на ребросклеивание и шпонопочинку, а другая — сразу на сортировку в соответствии с требованиями ГОСТ 3916.1-96 или требованиями заказчика. Неформатный, кусковой и оставшийся от обрезки шпон отправляется на ребросклеивание вдоль волокон на внутренние слои, а после обрезки поперёк — на линию усовки.
7) Склеивание шпона на «ус»
Склеенный на «ус» поперёк волокон шпон идёт на внутренние слои большеформатной фанеры
8) Ребросклеивание шпона
Для ребросклейки используются станки с подачей шпона вдоль и поперёк древесных волокон
9) Починка шпона
В починку шпона идут полоски шпона шириной до 49 мм, они подбираются по направлению волокон, цвету и породе древесины, толщине относительно требующих починки листов и плотно держатся в шпоне.
10) Приготовление и нанесение клея
Рецептура приготовления клея — ноу-хау любого фанерного завода, а наносится клей на шпон клеенаносящими станками, с помощью рифлёных металлических барабанов строго цилиндрической формы.
11) Сборка пакетов
Шпон с нанесенным клеем отправляют в наборку, где собираются пакеты, которые, проходя холодную подпрессовку, формируют будущие листы фанеры. Пакеты собираются в угольник, прижимаясь к упорам с двух сторон наборного стола. После холодной подпрессовки пакеты отправляют в загрузку горячего пресса.
12) Склеивание фанеры
Для склеивания фанеры используется горячий гидравлический пресс с электронной системой управления прессованием, механической загрузкой и выгрузкой. После пресса фанера развозится погрузчиком в стопы для выстройки. Стопы держатся в течение 24 часов в условиях цеха чтобы снять внутренние напряжения.
13) Обрезка фанеры и шлифование
В обрезке фанеры используются форматно-обрезные станки, а после обрезки её автопогрузчиком подают на сортировку или шлифовальный станок.
14) Сортировка, маркировка и упаковка.
Фанера подается на сортировочные площадки после обрезки и шлифования, где сортируется по ГОСТу 3916.1-96, после чего производится маркировка листов фанеры, упаковка её в стандартные транспортировочные пачки и маркировка пачек.
Производство в России
Фанера в России выпускается следующих основных форматов 1525х1525, 1220х2440, 2440х1220, 1250х2500, 2500х1250, 1500х3000, 3000х1500, 1525х3050 и 3050х1525мм. Различие в расположении длины и ширины относительно формата фанеры обозначает продольное или поперечное расположение волокон шпона по длинной стороне и указывает, что если формат заявлен как 1220х2440, то расположение слоёв шпона поперечное, а если 2440х1220 — продольное. Фанера с продольным расположением волокон шпона используется там, где требуется гибкость, а с поперечным — там, где требуется высокая жёсткость при изгибе.
Производство фанеры в России (млн. м³): 2002 г. — 1,8; 2003 г. — 2,0; 2004 г. — 2,2; 2005 г. — 2,6;
Фанерное производство в России расположено по большей части в привязке к регионам, богатым лесными ресурсами. Основная доля выпуска приходится на предприятия Северо-Западного федерального округа — около 35 % в общем объёме производства. В 2005 году экспорт составил 1,5 млн м³, то есть около 60 % всей произведённой в стране фанеры.
См. также
Примечания
Литература
- Григорьев М. А. Материаловедение для столяров, плотников и паркетчиков: Учебное пособие для ПТУ. — М.: Высшая школа, 1989. — 223 с. — 100 000 экз. — ISBN 5-06-000345-0.
- ГОСТ 3916.1-96 Фанера общего назначения с наружными слоями из шпона лиственных пород.
- ГОСТ 3916.2-96 Фанера общего назначения с наружными слоями из шпона хвойных пород.
- ГОСТ 13913-78 (ГОСТ на ДСП)
- ГОСТ 102-75 Фанера берёзовая авиационная.
- ГОСТ В-226-41 Дельта-древесина авиационная.
Ссылки
- Черкасов И. К. Фанера // БСЭ
wiki.sc
0 thoughts on “Фанера бакелитовая википедия – Фанера — Википедия”